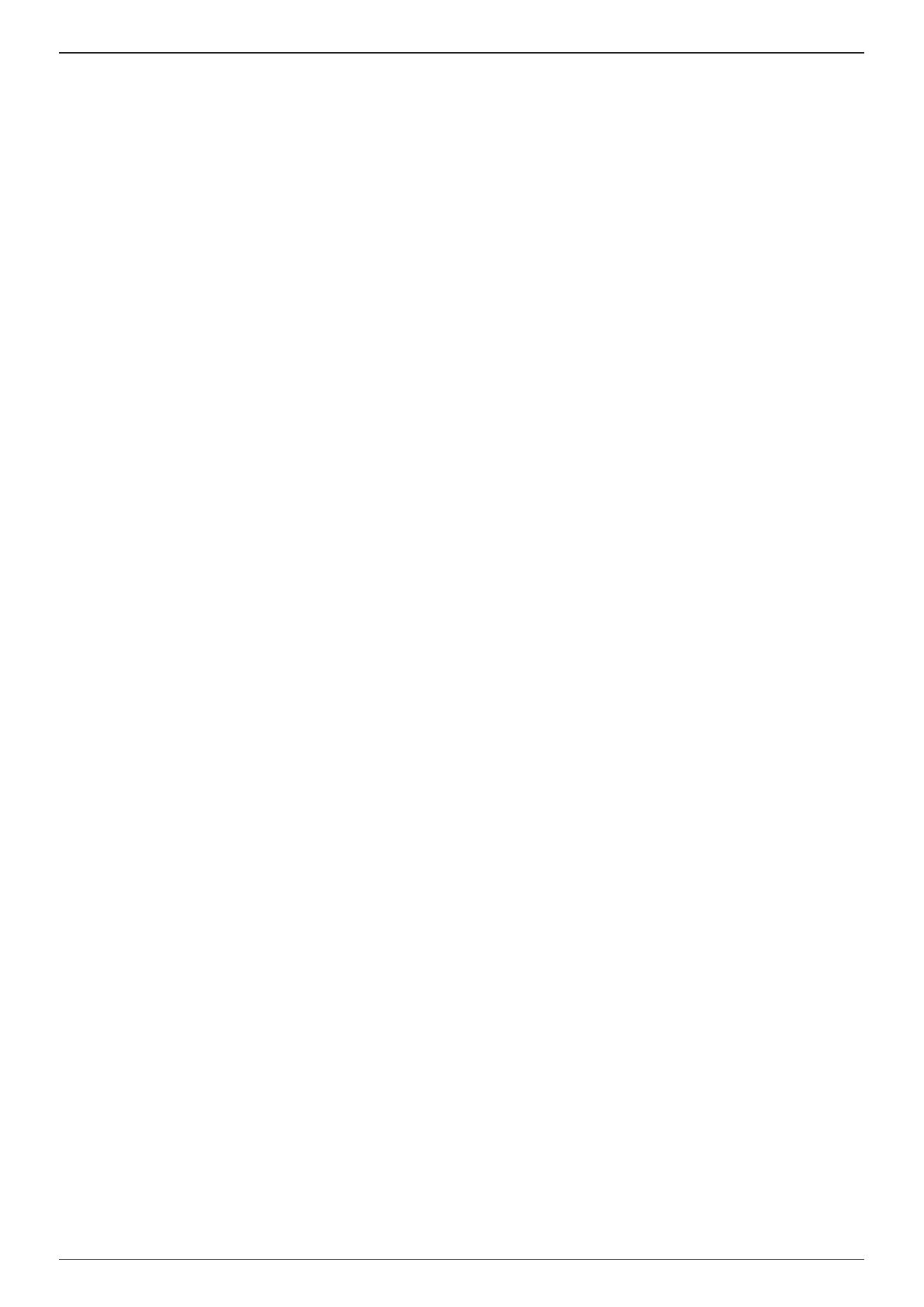
1. SAFETY DEFINITIONS ................................................................................................................................................... 4
1.1 GENERAL SAFETY RULES .......................................................................................................................................................................... 4
1.2 PROJECTILE HAZARDS .............................................................................................................................................................................. 4
1.3 OPERATING HAZARDS ............................................................................................................................................................................... 5
1.4 REPETITIVE MOTIONS HAZARDS............................................................................................................................................................ 5
1.5 ACCESSORY HAZARDS .............................................................................................................................................................................. 5
1.6 WORKPLACE HAZARDS ............................................................................................................................................................................. 5
1.7 NOISE HAZARDS .......................................................................................................................................................................................... 5
1.8 VIBRATION HAZARDS................................................................................................................................................................................. 6
1.9 ADDITIONAL SAFETY INSTRUCTION FOR PNEUMATIC POWER TOOLS ................................................................................... 6
2. SPECIFICATIONS ............................................................................................................................................................ 7
2.1 PLACING TOOL SPECIFICATION .............................................................................................................................................................. 7
2.2 TOOL DIMENSIONS ..................................................................................................................................................................................... 7
3. INTENT OF USE .............................................................................................................................................................. 8
4.1 AIR SUPPLY .................................................................................................................................................................................................... 8
4.2 STROKE ADJUSTMENT ............................................................................................................................................................................... 9
4.3 PRINCIPLE OF OPERATION ....................................................................................................................................................................... 9
5. NOSE ASSEMBLIES ......................................................................................................................................................10
5.1 FITTING INSTRUCTIONS .......................................................................................................................................................................... 10
5.2 SERVICE INSTRUCTIONS .........................................................................................................................................................................10
5.3 74200 NOSE ASSEMBLY COMPONENTS ............................................................................................................................................10
6. SERVICING THE TOOL..................................................................................................................................................13
6.1 DAILY SERVICING ....................................................................................................................................................................................... 13
6.2 WEEKLY SERVICING ...................................................................................................................................................................................13
6.3 SERVICE KIT ..................................................................................................................................................................................................13
6.4 MAINTENANCE ........................................................................................................................................................................................... 14
6.5 PNEUMATIC CYLINDER ............................................................................................................................................................................ 14
6.6 ROD GUIDE .................................................................................................................................................................................................. 14
6.7 TRIGGER ........................................................................................................................................................................................................ 14
6.8 SWIVEL AIR INLET (74200-12700) ........................................................................................................................................................ 15
6.9 DIFFERENTIAL VALVE................................................................................................................................................................................15
6.10 HEAD ASSEMBLY .......................................................................................................................................................................................15
6.11 REAR CASING .............................................................................................................................................................................................. 15
6.12 DISTRIBUTOR ..............................................................................................................................................................................................15
6.13 HYDRAULIC PISTON & AIR MOTOR ASSEMBLY (74200-12610) .................................................................................................15
6.14 MOLYKOTE 55m SAFETY DATA ............................................................................................................................................................. 17
6.15 PROTECTING THE ENVIRONMENT .......................................................................................................................................................17
7. GENERAL ASSEMBLIES ...............................................................................................................................................18
7.1 GENERAL ASSEMBLY OF BASE TOOL 74200-12000 .......................................................................................................................18
7.2 GENERAL ASSEMBLY PARTS LIST 74200-12000 ..............................................................................................................................19
8. PRIMING ......................................................................................................................................................................20
8.1 OIL DETAILS ................................................................................................................................................................................................. 20
8.2 HYSPIN®VG 32 OIL SAFETY DATA .........................................................................................................................................................20
8.3 PRIMING PROCEDURCE ...........................................................................................................................................................................20
9. FAULT DIAGNOSIS ....................................................................................................................................................... 21
10. EC DECLARATION OF CONFORMITY .......................................................................................................................... 23
11. UK DECLARATION OF CONFORMITY .........................................................................................................................24
12. PROTECT YOUR INVESTMENT! ...................................................................................................................................25
3
ORIGINAL INSTRUCTION ENGLISH